Continuous roller conveyor - type "PAP"
Blast wheel systems with a roller conveyor are called "PAP" ( Profiles And Plates). The workpieces are mostly made of steel or concrete plates and steel profiles and are transported through the blasting room on a roller conveyor. In the blasting room, blasting media are fired at the workpieces that comes from the blasting wheels. These centrifugal wheels are arranged according to the application so that an optimal blasting result is guaranteed. The speed of the transport speed of the roller conveyor can be adjusted by means of a frequency inverter. This allows the jet blast intensity (duration of jet blast impact per area) and process time to be adjusted.
A possible work cycle is as follows:
• Workpieces are placed outside the machine on the infeed side on the transport rollers or a side of the loading conveyor (if available). Loading is carried out manually, with a suitable lifting device (overhead conveyor, bridge crane or similar) or automatically. An Integration into a continuously working conveyor system is also possible.
• The workpieces are automatically transported through the machine from the infeed side and are continuously blasted. There is a sensor at the entrance lock that detects the presence (or absence) of workpieces and stops the blasting media supply if no workpieces are detected (in order to reduce the blasting time without a workpiece to a minimum). The supply of blasting media to the blasting wheels is also interrupted when the transport system stops.
• The amount of abrasive is set and controlled by an electro-pneumatically controlled valve. From there it is directed at the center of the blower wheel, from where it is fed through the distributor to the blower wheel blades. The rotation blades spin the blasting media onto the components to be cleaned or deburred.
• The mixture of blasting media, burrs, sand deposits, T tinder and/or other impurities ends up in the lower part of the machine (system hopper). From there it is transported to the bucket elevator. This material transport is carried out by longitudinal and transverse screw conveyors or a longitudinal screw conveyor and a vibrating screen (upstream blasting media separation of larger contaminants). The combination depends on the particular blasting task and must be discussed in detail.
• From the bucket elevator, the mixture is transported up to the blasting media preparation (air sifting). (If steel blasting media is to be separated from cast sand, a special magnetic separator is also used). The air separation separates dust and impurities from the clean and reusable blasting media.
• The coarser impurities are discharged from the closed circuit through a downpipe. The clean blasting media is continuously refed into the silos. From there it is returned to the blasting wheels via the control valve, which closes the blasting media cycle.
• The extraction of dust from the blasting chamber and from the abrasive preparation is carried out by a central exhaust air and filter system.
• After the blasting process, the workpieces pass through the discharge chamber. There the components can optionally be brushed off or blown off. Depending on the component geometry, a cleaning process is offered optionally. The position of the blow-off device and rotary brush can be adjusted by means of a push button. An automatic adjustment of the cleaning height is also possible as an option.
• On the outlet side, the components can either be carried out manually, with a suitable lifting device (overhead conveyor, bridge crane or similar) or automatically. An Integration into a continuously working conveyor system is also possible.
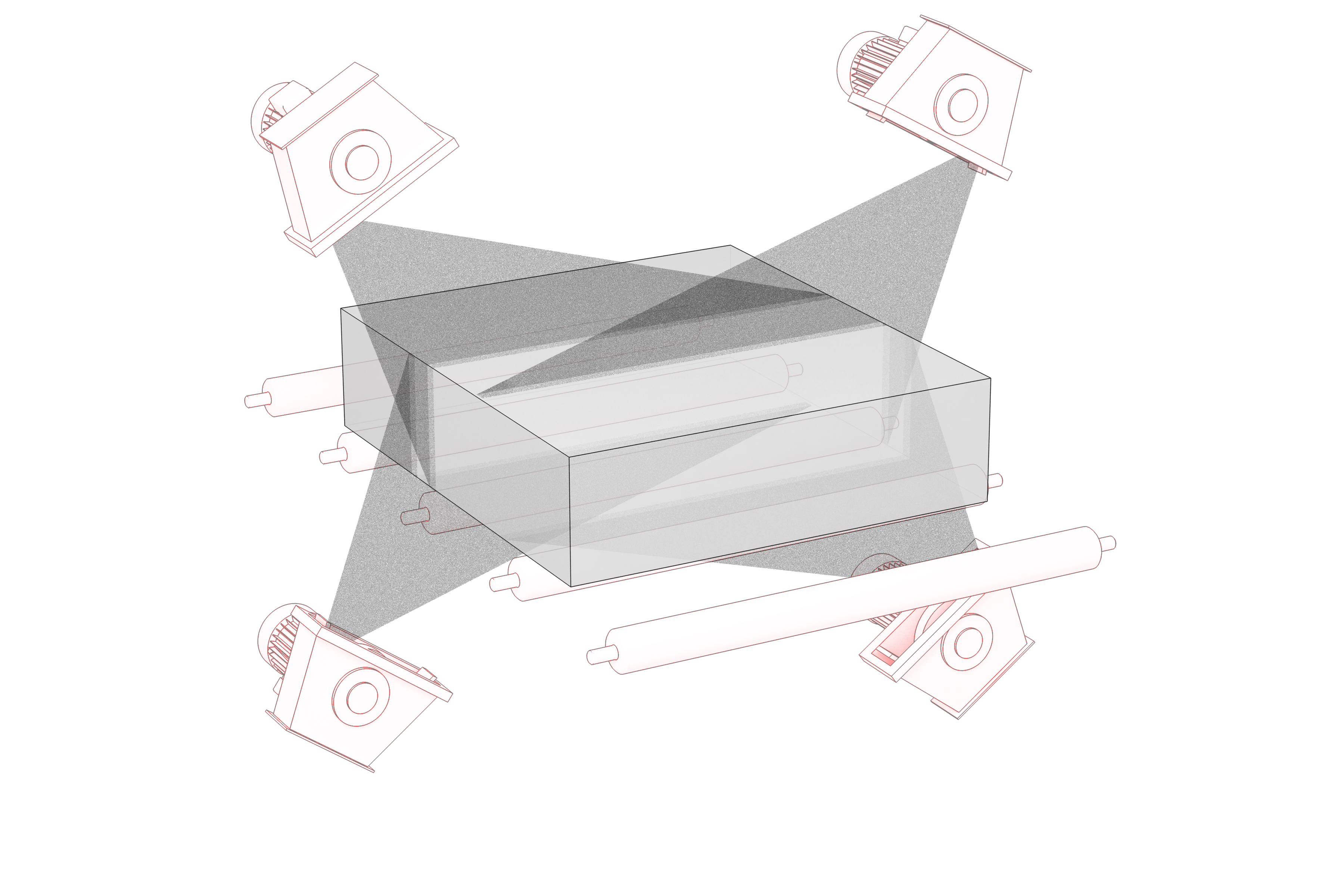
Machine type | PAP6x6 | PAP10x7 | PAP15x6 | PAP20x5 | PAP22x5 | PAP25x7 | PAP32x6 | PAP42x5 |
---|
Max. Sheet width [mm] | 600 | 1000 | 1500 | 2000 | 2200 | 2500 | 3200 | 4200 |
Max. Profile height [mm] | 600 | 700 | 600 | 500 | 500 | 700 | 600 | 500 |
Load capacity of the roller conveyor [kg / m] | 450 | 800 | 800 | 1000 | 1000 | 1200 | 1400 | 1600 |
Power of the turbine [ kW ] | 4x5,5 4x7,5 | 4x7,5 | 4x7,5 4x11 | 4x11 4x15 | 6x11 6x15 | 6x11 6x15 | 8x11 8x15 | 10x11 10x15 |
Rotary brush abrasive removal | * | * | * | X | X | X | X | X |
Blow-off fan | X | X | X | X | X | X | X | X |
| | | | | | | | |
| | | | | | | | |
*optional | | | | | | | | |
OPTIONEN |
Options frequency control of the centrifugal wheels Electrical control valves for program-specific dosing of blasting media Magnetic separator in blasting media processing Automatic blasting agent replenishment Blow-off fan for removal of blasting media with electrical and automated height adjustment Rotary brush for removal of blasting media with electrical and automated height adjustment Carbide centrifugal wheels Protective devices |
Ablation | paint stripping | removing rust |
descale | roughening | Solidifying / Shot-Peening |
Smoothing | Finishing | |